All You Need to Know About Mechanical Commercial Demolition
Demolition can be broken down into two main categories: residential and commercial. Residential is, as you’ve likely guessed, for homes and buildings that are considered living spaces. This includes homes and apartment buildings. Commercial demolition is for buildings used as offices, retail stores, and more.
Commercial demolition projects tend to be much larger than residential ones, and also require completely different planning and equipment. You can get even more specific under the umbrella of commercial demolition, which brings us to what we mean by “mechanical commercial demolition.”
Mechanical commercial demolition is the process of demolishing buildings with the help of mechanical tools. Mechanical demolition workers break the buildings down into smaller, more manageable pieces that are sorted to be recycled or discarded.
What Type of Equipment Does Commercial Demolition Require?
The complexity of commercial demolition is largely due to the equipment that is involved in the process. Here are the main pieces of equipment a commercial demolition contractor will use for your project.
High-Reach Excavators
All kinds of attachments go along with an excavator making it an incredibly versatile piece of machinery. The attachments can be used to demolish drywall, concrete, steel, and more.
Demolition Cranes
This is where your vision of a wrecking ball comes into play, but it’s more likely that your demolition company will use a high-reach excavator to get the job done. However, the crane may be useful in removing heavy equipment from a demo site or setting up protective barriers to minimize the spread of dust and debris.
Concrete Crushers
Concrete is the number one material that is recycled in a demolition project and can help offset some of the costs of the project. Many Portland demolition contractors will divert concrete from landfills by using concrete crushers.
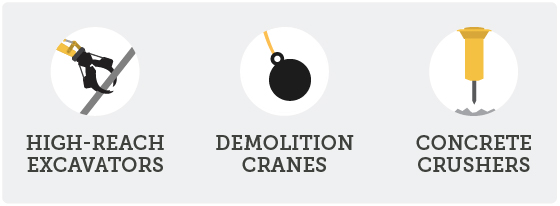
Are Permits Required for Mechanical Commercial Demolition?
Different kinds of permits are required for a mechanical commercial demolition project, and they can vary depending on the specifics of the project as well as the location of the building that’s being demolished.
One important step that must be taken is notifying the state department before the demolition if there is any chance that the building being demolished may contain a specific amount of asbestos. This is noted in the National Emission Standards for Hazardous Air Pollutants as part of the Clean Air Act and must be followed.
It is key that you have all the necessary permits before starting any demo. A professional in the business will be able to take a look at your project and know exactly what permits you need to do everything in adherence to the federal, state, and local laws.
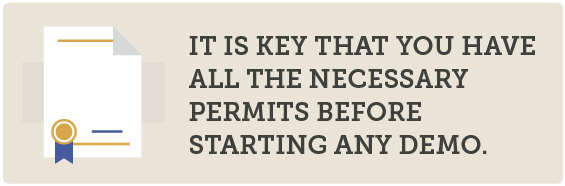
What Happens With the Materials From the Demolition?
Mechanical demolition workers break the commercial structure down into smaller pieces that are then sorted into two different categories: recycle or discard. Elder Demolition works to salvage building materials that clients can recycle, reuse, and sell. This is an eco-friendly approach to commercial demolition that gives materials a longer life while also reducing landfill waste, landfill costs, and overall project costs.